Quality assurance of Aidibath bathroom products
Understanding Quality Assurance for Aidibath Bathroom Products
Quality Assurance (QA) is a systematic process vital for ensuring that products meet established quality standards, particularly crucial in the bathroom product industry where durability and safety are of utmost importance. QA encompasses all stages of product development, from design to manufacturing, ensuring that each product aligns with the desired quality benchmarks. For Aidibath, a brand committed to delivering superior bathroom solutions, consistent quality assurance is non-negotiable as it directly influences the product's longevity and safety, which are key concerns for consumers.
The significance of QA in the bathroom product industry extends beyond basic compliance; it plays a critical role in reducing defects, enhancing customer satisfaction, and ensuring regulatory adherence. By identifying and rectifying potential issues early in the production process, QA helps in minimizing costs associated with product recalls or repairs. Furthermore, effective QA practices help Aidibath in catering to diverse customer needs, ensuring that their products remain safe, functional, and reliable for varied consumer requirements.
Key Components of Quality Assurance in Manufacturing
Quality Assurance in manufacturing heavily relies on a well-established Quality Management System (QMS). This system comprises a comprehensive set of policies, processes, and procedures designed to maintain and improve the quality of products during the manufacturing phase. A robust QMS forms the backbone of QA by facilitating consistent checks and balances throughout production, thus ensuring that the final product meets predefined standards. In essence, the QMS provides the blueprint for maintaining an efficient production line that prioritizes quality at every step.
Equally important in this process are inspection and testing protocols. These protocols are crucial components of ensuring that each product is thoroughly vetted for defects and functionality. Typically, this involves both pre-production checks and post-production testing. Pre-production checks are designed to identify potential issues before manufacturing begins, thereby preventing defects at their origin. Post-production testing, on the other hand, focuses on ensuring that finished products function correctly and adhere to quality specifications. By embedding comprehensive inspection and testing protocols, manufacturers can significantly reduce the incidence of defects, leading to increased customer satisfaction and reduced costs associated with recalls or reworks.
Top Quality Assurance Practices for Aidibath Bathroom Products
Implementing Standard Operating Procedures (SOPs) is fundamental for maintaining quality in manufacturing Aidibath bathroom products. SOPs ensure consistency by providing each team member with a structured guide on the manufacturing process. They outline each step required to produce products to meet established quality standards. SOPs help in reducing variations, preventing errors, and ensuring that every product meets the necessary specifications. Furthermore, they enable the identification and correction of deviations swiftly, thereby minimizing the risk of defects.
Equally important is the emphasis on employee training and development, which plays a pivotal role in enhancing product quality and reducing errors. Training programs equip staff with the necessary skills and knowledge to efficiently carry out quality assurance tasks. Through regular training sessions, employees learn the latest industry standards and technological advancements in bathroom product manufacturing. By investing in staff development, the company not only fosters a knowledgeable workforce but also ensures that quality assurance processes are effectively implemented and adhered to, resulting in superior product quality and increased customer satisfaction. Through these practices, Aidibath can maintain and improve its reputation for delivering high-quality bathroom products.
Product Showcase: Aidibath Bathroom Products
Europe High Toilet Disable People Hospital Use
Aidibath offers products like the Europe High Toilet for Disable People, which excels in accessibility while maintaining high-quality design and functionality. This product is ideal for various settings such as hospitals and care facilities. It underscores Aidibath's dedication to inclusivity where comfort and quality are paramount.
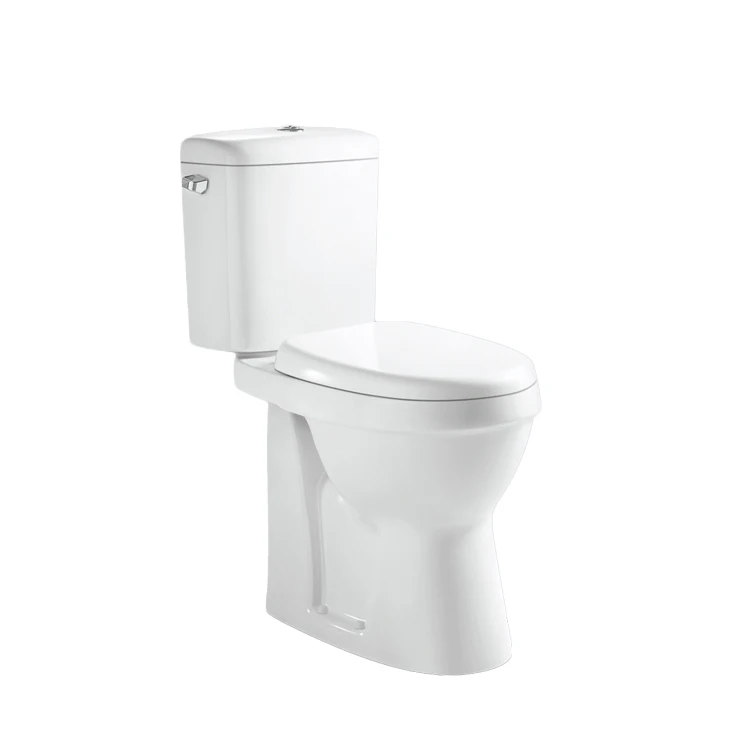
Cheapest Africa India Two Piece Toilet Sets
Targeting affordability without sacrificing quality, the cheapest Africa India Two Piece Toilet Sets are proof of Aidibath's commitment to serving emerging markets. This product meets consumer needs with competitive pricing and reliable operation.
Square Shape Rimless Toilet
The Square Shape Rimless Toilet represents innovation in bathroom design. This product features an easy-to-clean design without compromising aesthetics, catering to modern consumer desires for function and style.
Medyag New Tornado Wall Hung Toilet
The Medyag New Tornado Wall Hung Toilet features advanced flushing technology to optimize performance. This product highlights Aidibath's focus on creating efficient, high-performance washroom solutions.
Wall Hung Toilet with Concealed Water Tank
By combining elegance with practicality, the Wall Hung Toilet with Concealed Water Tank offers space-saving solutions without neglecting standards of water efficiency. This product is ideal for homes and businesses focused on conservation and design.
These products embody Aidibath's expertise in creating high-quality, accessible bathroom solutions suitable for a range of applications around the world.
The Role of Customer Feedback in Quality Assurance
Gathering customer feedback is vital for gauging satisfaction and identifying areas for improvement. Aidibath uses surveys, reviews, and direct communication channels to collect insights from its clientele. This feedback loop allows the company to assess how well its products meet customer expectations and where enhancements can be made. Engaging with customers helps the company stay connected with its market, continually innovate, and adapt to changing desires and needs.
Based on collected feedback, implementing changes is crucial for maintaining a robust quality assurance loop. Aidibath uses real user experiences to drive product and practice modifications, ensuring the continuous improvement of its offerings. This active response to feedback not only enhances product quality but also boosts customer satisfaction by showing that the company values and prioritizes customer input. This approach enables Aidibath to remain competitive and build stronger relationships with its consumers by consistently delivering reliable and well-received bathroom solutions.
Challenges in Maintaining Quality Assurance
Maintaining consistent quality assurance in bathroom products involves overcoming several challenges. Common issues may include defects such as cracks or leaks, miscommunications in manufacturing processes, and variations in material quality. These problems can result in diminished product reliability, affecting customer satisfaction and brand reputation. In addition, fluctuating quality can lead to increased return rates and warranty claims, further straining resources.
To address and overcome these challenges, companies can implement a series of strategic measures. First, rigorous training programs for employees across the production line ensure that all staff are well-versed in quality standards and procedures. This knowledge helps reduce errors and improve overall manufacturing consistency. Additionally, investing in high-quality materials is crucial to guarantee the durability and performance of bathroom products. Lastly, conducting regular audits of production processes allows companies to identify and address non-compliance with standards proactively. By integrating these strategies, businesses can better maintain quality assurance and strengthen their position in the competitive bathroom product market.
Conclusion: The Future of Quality Assurance in Bathroom Manufacturing
As we look to the future of quality assurance in bathroom manufacturing, a noticeable trend is the integration of automation and data analytics. These advancements drive efficiencies in the manufacturing process, allowing for enhanced quality control measures. With the impact of technology, manufacturers can receive real-time feedback, enabling immediate adjustments to quality assurance practices. Adopting these innovations not only optimizes production but also ensures that high-quality standards are consistently met, fostering greater reliability and customer satisfaction in bathroom products.